Download product information now
The value chain of CCUS
HERMETIC Pumpen attaches great importance to the global CO2 emission targets. Today carbon capture utilization and storage in the food industry is one way to reach the goal. With thousands of pumps for CO2 as refrigerant, HERMETIC Pumpen is a leading pump manufacturer for CO2 applications.
CO2 / LCO2
Carbon capture
CO2 capture plays a crucial role in various industrial processes, with technologies for separating or capturing CO2 from flue gas streams being commercially available for many decades. The most advanced and widely used methods are chemical absorption and physical separation.
CO2 is separated from the output stream using appropriate technology as for example chemical solvents, or membranes based on the type of stream. It is also separated from other gases or air, also called as Direct Air Capture, or a concentrated source. Depending on the production sources, the CO2 will have different characteristics which can be categorized into:
- High purity CO2 streams production (e. g. from bioethanol or beer production processes) that directly produce an output stream of 96 to 100 % CO2 purity
- Medium purity CO2 streams production (e. g. from iron & steel or cement production processes) that directly produce an output stream of 20 to 50 %. CO2 from Hydrogen production out of Syngas or refinery processes is considered to be within the 30 to 45 % purity range
- Low purity CO2 streams production (e. g. from paper and pulp or glass production processes) that directly produce an output stream of < 20 %. In refineries, process heating and FCC unit produce low purity (3 to 20 %) streams of CO2
CO2 / LCO2
Carbon capture
CO2 capture plays a crucial role in various industrial processes, with technologies for separating or capturing CO2 from flue gas streams being commercially available for many decades. The most advanced and widely used methods are chemical absorption and physical separation.
CO2 is separated from the output stream using appropriate technology as for example chemical solvents, or membranes based on the type of stream. It is also separated from other gases or air, also called as Direct Air Capture, or a concentrated source. Depending on the production sources, the CO2 will have different characteristics which can be categorized into:
- High purity CO2 streams production (e. g. from bioethanol or beer production processes) that directly produce an output stream of 96 to 100 % CO2 purity
- Medium purity CO2 streams production (e. g. from iron & steel or cement production processes) that directly produce an output stream of 20 to 50 %. CO2 from Hydrogen production out of Syngas or refinery processes is considered to be within the 30 to 45 % purity range
- Low purity CO2 streams production (e. g. from paper and pulp or glass production processes) that directly produce an output stream of < 20 %. In refineries, process heating and FCC unit produce low purity (3 to 20 %) streams of CO2
CO2 / LCO2
Purification and Liquefaction
For efficient storage and a re-use of the captured CO2 purification and liquefaction processes are beneficial. The purification step includes a cleaning process to receive high purity CO2 streams. The liquefaction process step includes several compression and cooling stages. As a result, the CO2 is available as cooled liquid (now also named liquified CO2 / LCO2) and can now easily be transferred to a storage tank.
CO2 / LCO2
Transport LCO2 to tank
Requirement
Medium: | CO2 / LCO2 |
Delivery rate: | 1,5 m3/h |
Pumping head: | 20 m |
Operating temperature: | –25 °C |
Medium: | CO2 / LCO2 |
Delivery rate: | 4 m3/h |
Pumping head: | 25 m |
Operating temperature: | –32 °C |
Hermetic Solutions
Pump: | CAM 1/5 |
Motor: | AGX1.0 |
Pump type: | Multistage |
Pump nominal pressure: | 40 bar |
Material: | Ductil iron |
Pump: | CAM 1/5 |
Motor: | AGX1.0 |
Pump type: | Multistage |
Pump nominal pressure: | 25 bar |
Material: | Stainless steel |
CO2 / LCO2
Load- and unloading station
Requirement
Medium: | CO2 / LCO2 |
Delivery rate: | 40 m3/h |
Pumping head: | 38 m |
Operating temperature: | –27 °C |
Medium: | CO2 / LCO2 |
Delivery rate: | 50 m3/h |
Pumping head: | 40 m |
Operating temperature: | –25 °C |
Hermetic Solutions
Pump: | CNF 50-200 |
Motor: | CKPx12.0 |
Pump type: | Single stage |
Pump nominal pressure: | 25 bar |
Material: | Ductil iron |
Pump: | CNF 50-200 |
Motor: | CKPx12.0 |
Pump type: | Single stage |
Pump nominal pressure: | 25 bar |
Material: | Stainless steel |
CO2 / LCO2
Transport
The availability of infrastructure to transport LCO2 safely and reliably is essential for deployment of CCUS. The most common options for the large-scale transport of CO2 are via onshore / offshore pipeline and ship. Although, for short distances and small volumes, it can also be transported by truck or rail, but at higher cost per ton of CO2.
Transport by pipeline has been practiced for many years and is already deployed at large scale. While LCO2 is currently transported via trucks or ships in small quantities for use in the food and beverage industry, large-scale transportation of LCO2 by ship has not yet been experienced much but seems to have similarities to liquefied petroleum gas (LPG) and liquefied natural gas (LNG) shipping.
CO2 / LCO2
Transport for utilization
Requirement
Medium: | CO2 / LCO2 |
Delivery rate: | 3 m3/h |
Pumping head: | 35 m |
Operating temperature: | –29 °C |
Hermetic Solutions
Pump: | CAM 2/3 |
Motor: | AGX3.0 |
Pump type: | Multistage |
Pump nominal pressure: | 25 bar |
Material: | Stainless steel |
CO2 / LCO2
Pumping station for storage
Requirement
Medium: | CO2 / LCO2 |
Delivery rate: | 400 m3/h |
Pumping head: | 40 m |
Operating temperature: | –30 °C |
Hermetic Solutions
Pump: | CNFu 250-200-400 |
Motor: | N85Z-4 |
Pump type: | Single stage |
Pump nominal pressure: | 25 bar |
Material: | Stainless steel |
CO2 / LCO2
Utilization
Biogenic liquified CO2 can be used in many applications. We have selected 3 potential ones.
Food and beverages
The worldwide food and beverage industries consume about 11 Mt CO2 annually. It is one of the most established and common end uses of LCO2.
Some applications could be soft drinks, water, beer carbonation or the production of deoxygenated water. These industries require very high CO2 purity.
Greenhouses
In this application, CO2 is used in the artificially air renewing system. The CO2 can help to increase the plants growth rate by 15 to 40 %. The CO2 consumption depends on the crop type and on lighting control.
Another important use in agriculture is pest control, where CO2 is considered an alternative to products such as methyl bromide, phosphines and insecticides. It has the advantage of leaving no residues after treatment. The fumigating effect of carbon dioxide allows post-harvest treatment, especially in organic agriculture, increasing food safety and reducing production residues.
Fertilizers
The industrial production of fertilizers in the EU-27 accounted for 18,100 kt in 2019. Approximately 72 % of this production corresponds to nitrogenous fertilizers, which include urea and ammonium nitrate.
To minimize the total carbon footprint from global biomass production, it is crucial to use land efficiently by adopting modern and more sustainable agricultural practices.
Urea is one of the most known chemical products. It can be used as a chemical fertilizer in urea resins, urea – melamine resins and as an animal feed additive. The most common urea production method is reforming natural gas, producing carbon dioxide and ammonia. Comparing to the nitrates production, urea emits less CO2, but upon spreading, the situation is reversed, since urea releases the CO2 contained in its molecule.
Urea also often releases more N2O. Therefore, the life cycle carbon footprint is higher for urea than for nitrates. As CO2 is used during urea production, biogenic LCO2 represents an environmentally friendly alternative.
CO2 / LCO2
Storage
LCO2 is stored by injecting the captured LCO2 into a deep underground geological reservoir of porous rock. These reservoirs are sealed by an impermeable layer of rocks, preventing any upward migration or leakage to the atmosphere. Various types of reservoirs are suitable for CO2 storage, with deep saline formations and depleted oil and gas reservoirs having the largest capacity. These formations consist of layers of porous and permeable rocks saturated with salty water (brine) and are found in both onshore and offshore sedimentary basins. Depleted oil and gas reservoirs are porous rock formations that have trapped crude oil or gas for millions of years before extraction.
The injected LCO2 fills the pore space of the reservoir. The gas is usually compressed first to increase its density. The reservoir must be at depths greater than 800 meters to retain the CO2 in a dense liquid state. The LCO2 is permanently trapped in the reservoir through several mechanisms
- structural trapping by the seal
- solubility trapping where the CO2 dissolves in the brine water
- residual trapping where the CO2 remains trapped in pore spaces between rocks
- mineral trapping where the CO2 reacts with the reservoir rocks to form carbonate minerals (mineralization)
The trapping mechanism depends on the sites’ lifespan and geological conditions. Decades of experience in the LCO2 injection and storage help to better understand the characteristics and select the right trapping method.
It is also possible to store CO2 in basalts (igneous rocks) that have high concentrations of reactive chemicals. However, this method is in an early stage of development. The injected CO2 reacts with the chemical components to form stable minerals, trapping the CO2.
Global CO2 storage resources are considered to be well in excess of likely future requirements. Nevertheless, in many regions, significant assessment work is required to convert theoretical storage capacity into effective storage.
CO2 / LCO2
Carbon capture
CO2 capture plays a crucial role in various industrial processes, with technologies for separating or capturing CO2 from flue gas streams being commercially available for many decades. The most advanced and widely used methods are chemical absorption and physical separation.
CO2 is separated from the output stream using appropriate technology as for example chemical solvents, or membranes based on the type of stream. It is also separated from other gases or air, also called as Direct Air Capture, or a concentrated source. Depending on the production sources, the CO2 will have different characteristics which can be categorized into:
- High purity CO2 streams production (e.g. from bioethanol or beer production processes) that directly produce an output stream of 96–100% CO2 purity
- Medium purity CO2 streams production (e. g. from iron & steel or cement production processes) that directly produce an output stream of 20–50%. CO2 from Hydrogen production out of Syngas or refinery processes is considered to be within the 30–45% purity range
- Low purity CO2 streams production (e. g. from paper and pulp or glass production processes) that directly produce an output stream of < 20%. In refineries, process heating and FCC unit produce low purity (3–20%) streams of CO2
CO2 / LCO2
Carbon capture
CO2 capture plays a crucial role in various industrial processes, with technologies for separating or capturing CO2 from flue gas streams being commercially available for many decades. The most advanced and widely used methods are chemical absorption and physical separation.
CO2 is separated from the output stream using appropriate technology as for example chemical solvents, or membranes based on the type of stream. It is also separated from other gases or air, also called as Direct Air Capture, or a concentrated source. Depending on the production sources, the CO2 will have different characteristics which can be categorized into:
- High purity CO2 streams production (e.g. from bioethanol or beer production processes) that directly produce an output stream of 96–100% CO2 purity
- Medium purity CO2 streams production (e. g. from iron & steel or cement production processes) that directly produce an output stream of 20–50%. CO2 from Hydrogen production out of Syngas or refinery processes is considered to be within the 30–45% purity range
- Low purity CO2 streams production (e. g. from paper and pulp or glass production processes) that directly produce an output stream of < 20%. In refineries, process heating and FCC unit produce low purity (3–20%) streams of CO2
CO2 / LCO2
Purification and Liquefaction
For efficient storage and a re-use of the captured CO2 purification and liquefaction processes are beneficial. The purification step includes a cleaning process to receive high purity CO2 streams. The liquefaction process step includes several compression and cooling stages. As a result, the CO2 is available as cooled liquid (now also named liquified CO2 / LCO2) and can now easily be transferred to a storage tank.
CO2 / LCO2
Transport LCO2 to tank
Requirement
Medium: | CO2 / LCO2 |
Delivery rate: | 1,5 m3/h |
Pumping head: | 20 m |
Operating temperature: | –25 °C |
Medium: | CO2 / LCO2 |
Delivery rate: | 4 m3/h |
Pumping head: | 25 m |
Operating temperature: | –32 °C |
Hermetic Solutions
Pump: | CAM 1/5 |
Motor: | AGX1.0 |
Pump type: | Multistage |
Pump nominal pressure: | 40 bar |
Material: | Ductil iron |
Pump: | CAM 1/5 |
Motor: | AGX1.0 |
Pump type: | Multistage |
Pump nominal pressure: | 25 bar |
Material: | Stainless steel |
CO2 / LCO2
Load- and unloading station
Requirement
Medium: | CO2 / LCO2 |
Delivery rate: | 40 m3/h |
Pumping head: | 38 m |
Operating temperature: | –27 °C |
Medium: | CO2 / LCO2 |
Delivery rate: | 50 m3/h |
Pumping head: | 40 m |
Operating temperature: | –25 °C |
Hermetic Solutions
Pump: | CNF 50-200 |
Motor: | CKPx12.0 |
Pump type: | Single stage |
Pump nominal pressure: | 25 bar |
Material: | Ductil iron |
Pump: | CNF 50-200 |
Motor: | CKPx12.0 |
Pump type: | Single stage |
Pump nominal pressure: | 25 bar |
Material: | Stainless steel |
CO2 / LCO2
Transport
The availability of infrastructure to transport LCO2 safely and reliably is essential for deployment of CCUS. The most common options for the large-scale transport of CO2 are via onshore / offshore pipeline and ship. Although, for short distances and small volumes, it can also be transported by truck or rail, but at higher cost per ton of CO2.
Transport by pipeline has been practiced for many years and is already deployed at large scale. While LCO2 is currently transported via trucks or ships in small quantities for use in the food and beverage industry, large-scale transportation of LCO2 by ship has not yet been experienced much but seems to have similarities to liquefied petroleum gas (LPG) and liquefied natural gas (LNG) shipping.
CO2 / LCO2
Transport for utilization
Requirement
Medium: | CO2 / LCO2 |
Delivery rate: | 3 m3/h |
Pumping head: | 35 m |
Operating temperature: | –29 °C |
Hermetic Solutions
Pump: | CAM 2/3 |
Motor: | AGX3.0 |
Pump type: | Multistage |
Pump nominal pressure: | 25 bar |
Material: | Stainless steel |
CO2 / LCO2
Pumping station for storage
Requirement
Medium: | CO2 / LCO2 |
Delivery rate: | 400 m3/h |
Pumping head: | 40 m |
Operating temperature: | –30 °C |
Hermetic Solutions
Pump: | CNFu 250-200-400 |
Motor: | N85Z-4 |
Pump type: | Single stage |
Pump nominal pressure: | 25 bar |
Material: | Stainless steel |
CO2 / LCO2
Utilization
Biogenic liquified CO2 can be used in many applications. We have selected 3 potential ones.
Food and beverages
The worldwide food and beverage industries consume about 11 Mt CO2 annually. It is one of the most established and common end uses of LCO2.
Some applications could be soft drinks, water, beer carbonation or the production of deoxygenated water. These industries require very high CO2 purity.
Greenhouses
In this application, CO2 is used in the artificially air renewing system. The CO2 can help to increase the plants growth rate by 15 to 40 %. The CO2 consumption depends on the crop type and on lighting control.
Another important use in agriculture is pest control, where CO2 is considered an alternative to products such as methyl bromide, phosphines and insecticides. It has the advantage of leaving no residues after treatment. The fumigating effect of carbon dioxide allows post-harvest treatment, especially in organic agriculture, increasing food safety and reducing production residues.
Fertilizers
The industrial production of fertilizers in the EU-27 accounted for 18,100 kt in 2019. Approximately 72 % of this production corresponds to nitrogenous fertilizers, which include urea and ammonium nitrate.
To minimize the total carbon footprint from global biomass production, it is crucial to use land efficiently by adopting modern and more sustainable agricultural practices.
Urea is one of the most known chemical products. It can be used as a chemical fertilizer in urea resins, urea – melamine resins and as an animal feed additive. The most common urea production method is reforming natural gas, producing carbon dioxide and ammonia. Comparing to the nitrates production, urea emits less CO2, but upon spreading, the situation is reversed, since urea releases the CO2 contained in its molecule.
Urea also often releases more N2O. Therefore, the life cycle carbon footprint is higher for urea than for nitrates. As CO2 is used during urea production, biogenic LCO2 represents an environmentally friendly alternative.
CO2 / LCO2
Storage
LCO2 is stored by injecting the captured LCO2 into a deep underground geological reservoir of porous rock. These reservoirs are sealed by an impermeable layer of rocks, preventing any upward migration or leakage to the atmosphere. Various types of reservoirs are suitable for CO2 storage, with deep saline formations and depleted oil and gas reservoirs having the largest capacity. These formations consist of layers of porous and permeable rocks saturated with salty water (brine) and are found in both onshore and offshore sedimentary basins. Depleted oil and gas reservoirs are porous rock formations that have trapped crude oil or gas for millions of years before extraction.
The injected LCO2 fills the pore space of the reservoir. The gas is usually compressed first to increase its density. The reservoir must be at depths greater than 800 meters to retain the CO2 in a dense liquid state. The LCO2 is permanently trapped in the reservoir through several mechanisms
- structural trapping by the seal
- solubility trapping where the CO2 dissolves in the brine water
- residual trapping where the CO2 remains trapped in pore spaces between rocks
- mineral trapping where the CO2 reacts with the reservoir rocks to form carbonate minerals (mineralization)
The trapping mechanism depends on the sites’ lifespan and geological conditions. Decades of experience in the LCO2 injection and storage help to better understand the characteristics and select the right trapping method.
It is also possible to store CO2 in basalts (igneous rocks) that have high concentrations of reactive chemicals. However, this method is in an early stage of development. The injected CO2 reacts with the chemical components to form stable minerals, trapping the CO2.
Global CO2 storage resources are considered to be well in excess of likely future requirements. Nevertheless, in many regions, significant assessment work is required to convert theoretical storage capacity into effective storage.
HERMETIC product range for your CO2 applications
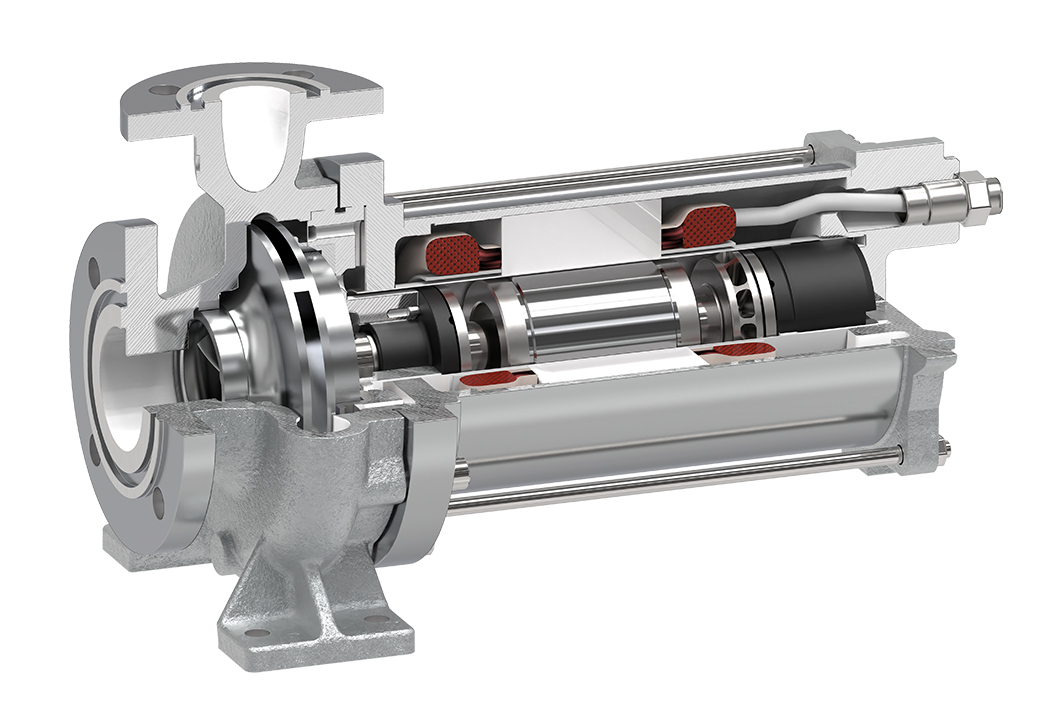
CNF stainless steel
Delivery rate: | max. 85 m3/h |
Pumping head: | max. 90 m |
Pressure rating: | PN1 6 / PN 25 |
Operating temperature: | –90 °C to +30 °C |
Motor: | AGX 3.0 – CKPx 19.0 |
Material: | Stainless steel 1.4408 |
Customisation
If you cannot find a suitable pump series? We are happy to help you with a customised solution regardless of the quantity. Please contact us for further information.
Safe pump technology from HERMETIC contributes to Carbon Capture and Storage (CCS) value chain
Safe pump technology from HERMETIC contributes to Carbon Capture and Storage (CCS) value chain
HERMETIC canned motor pumps in use in project “Greensand” In March of 2023, CO₂ has been stored underground for the first time worldwide, and on a transnational basis, within the scope of project “Greensand” to counteract the effects of climate change. This project demonstrates how CO₂ emission sources can be combined with suitable CO₂ storage areas.
Your contact to us
Would you like to find out more about Carbon Capture Utilization and Storage (CCUS) applications?
Simply fill out our contact form and our team will assist you with all your questions and concerns.
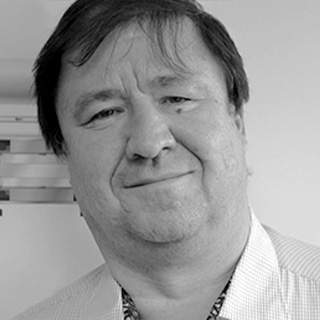
Alexei Khazanov
Sales / Refrigeration Pumps
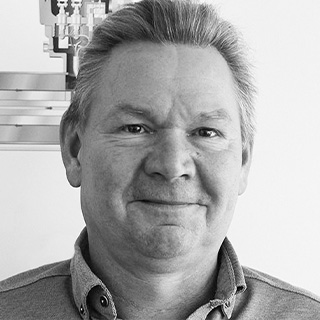
Christoph Galli
Sales / Refrigeration Pumps